|
|
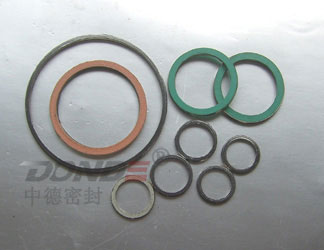
Exhaust Manifold With Catalytic
Converter
|
Abstract: |
A spiral-wound gasket includes a plurality of tightly
wound metal windings to form a core. The windings each have
a Chervon cross-section, wherein V-notched undulations of
each winding registers with an adjacent winding at said
notches. The edges of the windings are welded to form a
pre-assembled integral composite that is installed into a
J-shaped outer wrap or cover. Finally, the cover is closed
about the core so as to entirely cover and encapsulate the
core. In a preferred form, both the core and outer cover are
formed of stainless steel materials. |
Claim: |
What is claimed is:
1. A spiral-wound gasket having a generally circular
cross-section comprising: a plurality of tightly wound metal
windings comprising a core of said gasket, said
metalwindings having a Chevron cross-section and being
welded at edges thereof to define an integral circular hoop;
said gasket further comprising a circumferential outer
cover; wherein said outer cover also comprises a metal, and
entirely covers saidexterior surfaces of said core to
incorporate an overlap of the ends of said outer cover.
2. The spiral-wound gasket of claim 1 wherein said core
comprises a stainless steel material.
3. The spiral-wound gasket of claim 1 wherein said
circumferential outer cover comprises a stainless steel
material for oxidation resistance.
4. The spiral-wound gasket of claim 1 wherein both said core
and said outer cover comprise stainless steel materials.
5. The spiral-wound gasket of claim 4 wherein said metal
winding comprises SAE 304 stainless steel for hardness and
spring characteristics.
6. The spiral-wound gasket of claim 5 wherein said outer
cover comprises SAE 301 stainless steel to provide a
relatively soft outer surface of said gasket.
7. The spiral-wound gasket of claim 6 wherein the
combination of said outer cover and said core comprises a
gasket, which retains resiliency in a temperature range of
1200.degree. F. to 1500.degree. F.
8. The spiral-wound gasket of claim 1 wherein said edges of
said metal windings are slightly radiused.
9. A method of making a metallic spirally-wound gasket
having a generally circular shaped cross-section comprising
steps of: (a) spirally coiling together a plurality of
strips of metal having a Chevron cross-section to form an
annular core ofsaid gasket, (b) welding the edges of said
strips together whereby said core defines a pre-assembled
unitary composite, (c) providing a second portion defining
an annular outer cover having a J-shaped cross-section, and
being sized to accommodate saidannular core, (d) inserting
said core into the trough of said J-shaped cross-section,
wherein said upper portion of said core is exposed, and (e)
wrapping the upstanding portion of said J-shaped outer cover
about the exposed portion of said core to fillyencapsulate
said core, whereby said J-shaped outer cover becomes air
O-shaped outer cover about said core.
10. The method of making a metallic spirally-wound gasket of
claim 8 wherein said core comprises an SAE 304 stainless
steel material.
11. The method of making a metallic spirally-wound gasket of
claim 9 wherein said outer core comprises an SAE 301
stainless steel material, and has ends, one of which
overlaps the other. |
Description: |
BACKGROUND OF THE INVENTION
1. Field of Invention
This invention relates to gaskets employed in vehicles, and
particularly to metallic gaskets employed in manifold
exhaust systems of vehicles.
2. Description of the Prior Art
Exhaust manifolds used in automotive vehicles are subject to
great variations in temperature, as well as to extreme
mechanical vibrations. As such, the gaskets associated with
exhaust manifolds and vehicle exhaust systems are known to
presentdifficult sealing challenges. Gaskets interposed
between exhaust connection parts are required to maintain
resilient sealing properties over extended periods of time,
and have an accompanying risk of exposing vehicular
occupants to carbon monoxidepoisoning if such gasket seals
are inadequate.
Choices of gasket materials used under such severe
conditions include metal-covered gaskets with soft core
members such as heat resistant fibers including asbestos and
ceramic fibers. More recently the use of expanded graphite
and/or micacovered by a metallic sheet has been popular.
Such metal-covered gaskets have provided relatively soft
core members that offer excellent heat resistance, while the
metallic coverings offer rigidity. However, such gaskets
have been subject to reductionof contact pressure between
connected parts over a period of time, along with
deterioration of sealing properties under conditions of
cyclic thermal expansion and vibrations, and thus recovery
properties of such composite material bodies have not held
upover time. In addition, graphite fillers used in such
gaskets have been subject to severe oxidation, which
compromises integrity of the gasket structures.
Spiral-wound gaskets have been offered to overcome issues of
resiliency, hence recovery, as well as oxidation. However,
most such spiral-wound gaskets have been formed of complex
structures, which are expensive to manufacture. As a result,
suchgaskets have not been feasible for many applications.
SUMMARY OF THE INVENTION
The present invention provides a new improved gasket
assembly that is simpler in construction, and relatively
less expensive to manufacture than spiral-wound gaskets of
the prior art. The improved gasket of this invention employs
a spiral-woundplurality of tightly bound-together windings
comprising a core or filler portion. The core windings
present a Chevron cross-section, intermittently spot welded
along its inside and outside circumferential diameters to
define an integral pre-formedcircular hoop. In a preferred
embodiment, the core is formed of a stainless steel
material. The core is covered by an outer circumferential
metal wrap that is somewhat softer than the resilient,
springy metal material of the core. In its preferredform,
the outer wrap also comprises a metal of stainless steel,
and entirely covers the exterior surfaces of the core to
avoid oxidation.
BRIEF DESCRIPTION OF THE DRAWINGS
FIG. 1 is a plan view of a spiral-wound gasket constructed
in accordance with a preferred embodiment of the present
invention.
FIG. 2 is a view along lines 2--2 of FIG. 1, depicting the
Chevron-shaped cross-section of the spiral-wound gasket.
FIG. 3 is a view demonstrating the manner in which the
gasket is constructed, particularly showing the core portion
of the gasket partially installed, and prior to being fully
wrapped by the outer cover portion.
FIG. 4 is an exploded cross-section of an exhaust pipe
assembly incorporating the same preferred embodiment of the
spiral-wound gasket of this invention.
DETAILED DESCRIPTION OF PREFERRED EMBODIMENTS
Referring initially to FIGS. 1 and 2, a metal spiral-wound
gasket 10 is shown to have the form of a rounded annulus, or
hoop, and includes a metal outer wrap or cover 12. An
interior metal filler or core 14 is formed of a plurality of
individualstrips of Chevron-shaped metal windings 16.
Referring now particularly to FIG. 3, it will be appreciated
by those skilled in the art of manufacturing spiral-wound
gaskets that the V-notched undulations 18 of each strip 16
serve to impart a collective rigidity to the plurality of
strips. In this particular preferred embodiment, the edges
20 of the layered individual strips 16 include a slight
radius as shown to avoid stress cracks in a pre-formed
resilient stainless steel core 14.
Also in the preferred embodiment of the subject invention,
the individual strips employed to form the windings are
preferably formed of a 304 stainless steel, which offers a
spring steel quality as well as a resilience unparalleled by
other typesof stainless steel. The core 14 is pre-assembled
to form a unitary composite having the noted shape of a
circular hoop, with spot welds (not shown) provided
intermittently along the circumferential outside diameter
portion 6 of the core 14, as well asalong the inside
diameter portion 8 thereof, to assure integrity of the core
14.
A method of forming the gasket 10 is described in reference
to FIG. 3. The composite core 14 is installed into the
bottom or trough portion 24 of a J-shaped cover 12 during
manufacture of the gasket 10. An upstanding portion 26 of
the J-shapedcover 12 is wrapped about the exposed upper
surface of the core 14 to form the O-shaped cross-sectioned
cover 12 depicted in FIG. 2. In a preferred form, the upper
extremity of the upstanding leg or portion 26 is wrapped
over the opposed end 27 of thecover 12 to form an overlapped
portion 22. The cover is preferably formed of a softer
stainless steel material, such as SAE 301.
Although the preferred orientation of the collective
V-notched undulations 18 of the Chevron-shaped metal
windings 16 is as depicted in FIG. 2 for the described
embodiment, other angular orientations may be suitable. The
use of stainless steel,however, is strongly recommended for
both core 14 and cover 12 in the present invention. Other
metals, for example aluminum, are too soft for the high
temperature, oxidation-prone environment of an exhaust
manifold. Indeed, with respect to materials assoft as
aluminum, there generally is no spring recovery available in
the relevant heat range; hence plastic deformation of the
gasket becomes a major issue.
FIG. 4 depicts an exemplary application of the spiral-wound
gasket 10 of the present invention. A pair of mating exhaust
flanges 30 and 32 is affixed to an exhaust pipe 34 as, for
example, in an exhaust manifold environment. The interior of
thepipe 36 is suitable for the conveyance of hot gases
having temperatures in a range of 1200.degree. F. to
1500.degree. F. The exhaust flange face 40 of the flange 30
contains a U-shaped or recessed groove 38 wherein the gasket
may be installed prior tothe mating of and the coupling of
the flanges together via bolts (not shown) which pass
through bolt apertures 44 and 46 for appropriate securement.
The groove 38 that accommodates the gasket 10 is preferred
because the fully metallic gasket 10 has a relatively low
incompressibility. Those skilled in the art will appreciate
that appropriate dimensional tolerancing will be
necessarilyvariable from application to application.
However, one preferred dimension for the gasket for
automotive passenger car use, as an example, includes a
cross-sectional diameter of 4.5 mm. The depth of the groove
38 is approximately 4 mm, leaving acompressibility dimension
of 0.5 mm. It will be noted that the flange face 42 of the
flange 32 that mates with the exhaust flange face 40 is flat
faced. Thus, for the dimensions set forth in the example,
there is no need for a groove or recess to becarried in the
flange face 42. |
Back
to Spiral Wound Exhaust Pipe Gasket
|